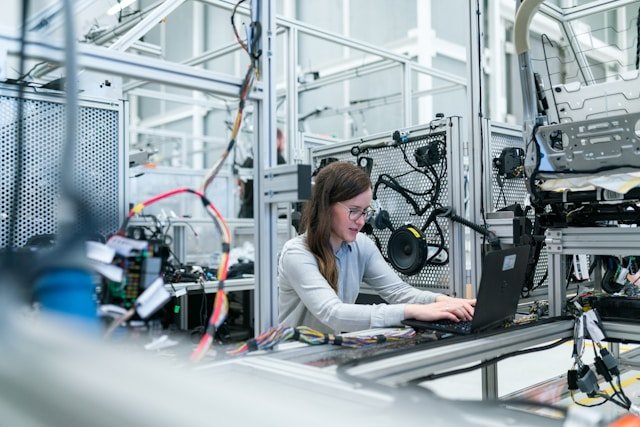
3 Smart Ways to Improve Operations at a Manufacturing Facility
- Business
- May 31, 2024
- No Comment
Manufacturing facilities are essential in many industries and serve as the backbone of corporations, driving productivity, innovation, and growth. To stay competitive, manufacturing facilities must optimize their operations and continually improve their processes. From streamlining processes to enhancing quality control, it’s essential to implement innovative strategies that improve efficiency. Let’s explore three intelligent ways to optimize operations at your manufacturing facility.
1: Invest in Metrology Equipment for Precise Measurement
Precision management is important in manufacturing because even the smallest deviation can lead to performance issues or product defects. Metrology equipment provides manufacturing plants with advanced capabilities for accurate and reliable measurement of parts and components. Investing in metrology equipment improves quality control, optimizes the overall manufacturing process, and makes compliance with industry standards much easier.
With quality control, metrology equipment makes it possible to precisely measure each component’s dimensions, surface finishes, and geometries throughout the production process so defective parts are found early. Through optimizing the overall manufacturing process, metrology data makes it possible to fine-tune manufacturing systems and improve efficiency while minimizing waste. Lastly, the strict regulatory requirements within most industries are better met while using metrology equipment to ensure compliance.
2: Use Lean Manufacturing Principles to Optimize Your Process
Lean manufacturing principles focus on eliminating waste and maximizing value throughout production. These principles include value stream mapping and JIT production. Value stream mapping involves identifying opportunities for process improvement and waste reduction by analyzing the entire production process for value-added and non-value-added activities. JIT, also known as Just-in-Time, production involves minimizing inventory levels and making sure that manufacturing plants are only producing goods when they are needed. JIT production can cut back on excess inventory, limit storage costs, and boost overall cash flow.
Kaizen events also focus on lean manufacturing principles and involve hosting focused workshops to address specific process issues with the team. Bringing in a cross-functional team can make it possible to find both issues and solutions that would have been found outside of one department.
3: Use Predictive Maintenance to Ensure Equipment Reliability
Equipment downtime hurts manufacturing operations and leads to production delays, decreased productivity, and mounting costs. Predictive maintenance focuses on data analytics and advanced monitoring techniques to determine when equipment failures will occur and before they occur. This makes it possible to maintain equipment by proactively performing maintenance.
From sensors and monitoring systems that collect real-time data on equipment performance and health to predictive models that forecast equipment failures, predictive maintenance keeps machines working longer and better than ever before. With predictive maintenance, you can reduce downtime, extend your equipment life, and optimize your maintenance scheduling.
Manufacturing facilities that prioritize these strategies are more likely to boost performance, increase efficiency, and maintain a competitive edge in the industry. Investing in metrology equipment, embracing lean manufacturing principles, and using predictive maintenance can enhance your operations, reduce costs, and ensure your facility is at the forefront of innovation. So, why wait? Start implementing these strategies today and see how they can improve your facility’s performance.